Automation at Designed Mouldings
![]() |
Automation at Designed MouldingsSee all Off-the-Shelf Solutions Australia-based Designed Mouldings is an injection moulding specialist, producing plastic caps and seals for customers in the packaging industry. The ChallengeThe Covid-19 pandemic led to border closures, causing disruptions to global supply chains. Companies in Australia turned to local manufacturers like Designed Mouldings for their production. After witnessing a spike in orders, Designed Mouldings examined their processes and found that the manual insertion of wads into plastic caps took a great deal of time. The company decided to automate the assembly process to reduce the cycle time and increase productivity.
Solution: using VGC10 vacuum gripperThe OnRobot VGC10 electric vacuum gripper was an obvious choice for this collaborative application. With unlimited customization to fit various needs, the small, lightweight gripper is perfect for tight spaces and can be redeployed to multiple tasks, thereby delivering a flexible automation system. The VGC10 gripper – integrated with a Techman cobot – works as a stand-alone system and does not require an external air supply or extra cabling and piping, speeding up deployment while reducing maintenance costs. This creates a collaborative application with a small footprint – one that can be easily moved and plugged in anywhere. Importantly, it is able to work safely alongside employees; no safety fence is needed. Setting up the VGC10 gripper was fairly quick. Designed Mouldings completed the installation and programming within just three to four days. “The OnRobot VGC10 gripper can easily complete a 20,000 product run in 24 hours – three times faster than if it were done manually. With a constant stream of jobs, we are expected to achieve ROI in six months,” said Paul Neumeyer, Managing Director of Designed Mouldings. The benefits of using VGC10The company has also seen a reduction in material waste by one to two percent, and employees are now relieved from tedious tasks, allowing them to focus on higher-value jobs. With the successful VGC10 implementation, Designed Mouldings is keen to automate other manual processes. Specifically, the company is looking to use the OnRobot RG2 gripper to assemble filters for hospitals. About Designed MouldingsDesigned Mouldings is an Australian-owned and operated company that was established in 1976 with the aim of servicing primarily the pharmaceutical industry with quality injection moulded components at internationally competitive prices. Our 2000m2 air-conditioned factory is located in the Southern Metropolitan area of Sydney Australia which was purposed built in 1992 for the manufacture of plastic injection moulded articles. Currently home to 18 injection moulding machines ranging in tonnage from 50-300 tonnes, we have the capability to mould single or multi-piece articles. |
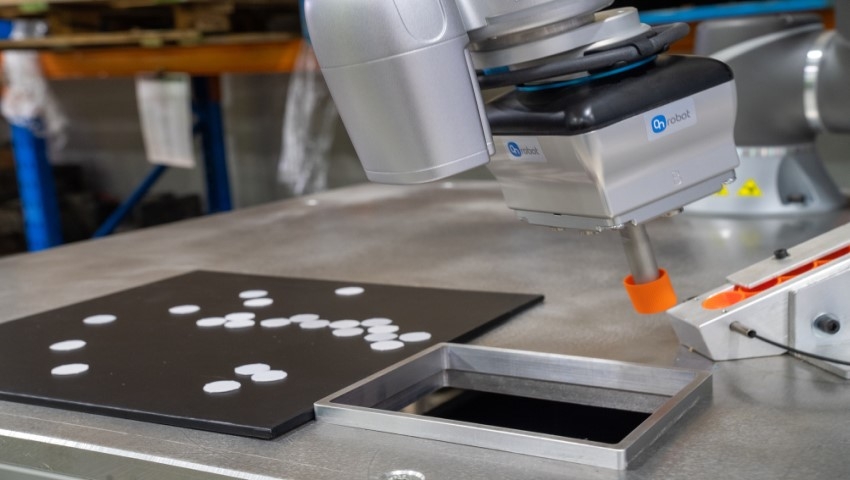
Automation at Designed Mouldings
Australia-based Designed Mouldings is an injection moulding specialist, producing plastic caps and seals for customers in the packaging industry.
The Challenge
The Covid-19 pandemic led to border closures, causing disruptions to global supply chains. Companies in Australia turned to local manufacturers like Designed Mouldings for their production. After witnessing a spike in orders, Designed Mouldings examined their processes and found that the manual insertion of wads into plastic caps took a great deal of time. The company decided to automate the assembly process to reduce the cycle time and increase productivity.
Solution: using VGC10 vacuum gripper
The OnRobot VGC10 electric vacuum gripper was an obvious choice for this collaborative application. With unlimited customization to fit various needs, the small, lightweight gripper is perfect for tight spaces and can be redeployed to multiple tasks, thereby delivering a flexible automation system.
The VGC10 gripper – integrated with a Techman cobot – works as a stand-alone system and does not require an external air supply or extra cabling and piping, speeding up deployment while reducing maintenance costs. This creates a collaborative application with a small footprint – one that can be easily moved and plugged in anywhere. Importantly, it is able to work safely alongside employees; no safety fence is needed.
Setting up the VGC10 gripper was fairly quick. Designed Mouldings completed the installation and programming within just three to four days.
“The OnRobot VGC10 gripper can easily complete a 20,000 product run in 24 hours – three times faster than if it were done manually. With a constant stream of jobs, we are expected to achieve ROI in six months,” said Paul Neumeyer, Managing Director of Designed Mouldings.
The benefits of using VGC10
The company has also seen a reduction in material waste by one to two percent, and employees are now relieved from tedious tasks, allowing them to focus on higher-value jobs.
With the successful VGC10 implementation, Designed Mouldings is keen to automate other manual processes. Specifically, the company is looking to use the OnRobot RG2 gripper to assemble filters for hospitals.
About Designed Mouldings
Designed Mouldings is an Australian-owned and operated company that was established in 1976 with the aim of servicing primarily the pharmaceutical industry with quality injection moulded components at internationally competitive prices. Our 2000m2 air-conditioned factory is located in the Southern Metropolitan area of Sydney Australia which was purposed built in 1992 for the manufacture of plastic injection moulded articles. Currently home to 18 injection moulding machines ranging in tonnage from 50-300 tonnes, we have the capability to mould single or multi-piece articles.
