When do you need robot vision?

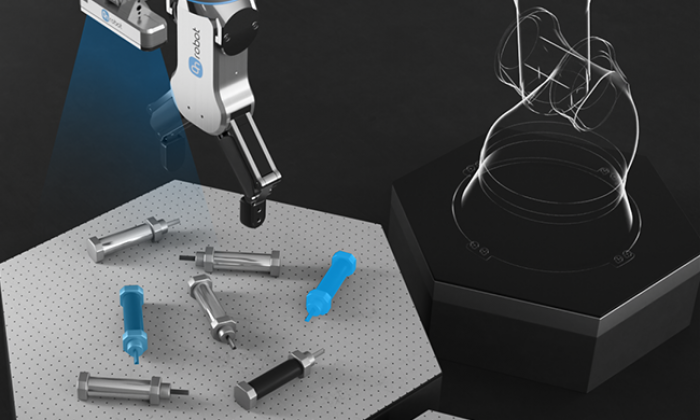
'I think we need robot vision' is a statement that can strike fear into the heart of even the most seasoned robotics specialists.
This is because of a widespread perception that robot vision systems—comprising cameras, robots and supporting software—are complex, expensive, difficult to integrate and not entirely reliable.
Thankfully, it doesn't have to be that way.
In fact, with the emergence of new technologies and falling costs, incorporating vision into your existing automation is now far more accessible; especially for cobot users.
In this blog post we'll look at the benefits of vision by comparing vision-enabled automation against 'blind' systems. We'll explore some of the different camera options available and the upsides and downsides of each. Finally, we'll dive into camera technology that can help you extract even more value from your cobot implementations.
Benefits of vision
Consider the complex set up that's required for a traditional 'blind' automation application to perform a simple pick & place task. The main challenge here is that objects have to be presented to your robots in exactly the same orientation and location every single time. This means installing costly fixtures and fittings and hardware such as bowl feeders, so that randomness is eliminated and your robots know precisely where the item to be picked is located.
Robots can perform superbly without vision, but what if you need to pick and place different objects? What if you want your automation to be capable of handling several types of objects arriving in different orientations? And what if you require rapid changeover times when switching between products?
In these scenarios, with flexibility and cost in mind, you should consider the benefits of adding robot vision—i.e., a camera and associated software—to your production lines. Vision eliminates the labor and capital costs associated with the addition of new hardware and fittings. Vision brings flexibility to your operations, enabling you to switch between different products easily. And vision dramatically reduces the time required to move between one product and another—a massive boon for busy manufacturers, especially in today's demanding, customized-production environment.
There are clear benefits to giving your cobot 'eyes,' but not all vision solutions are the same; variations in expense, flexibility, ease of use and software capabilities make a huge difference. So let's take a look at different camera types typically employed in automation scenarios.
Which D is for me?
Robot cameras come in three main flavors: 2D, 3D and 2.5D.
2D cameras are the cheapest of the bunch, but are the least versatile. Typically, 2D cameras determine length and width (X and Y axis), but are unable to determine height, which limits the number of applications they can support. On the plus side, they are reliable within these constraints.
With some clever mathematics, the performance of 2D cameras can be improved, but that tends to be an inconvenient, time-consuming and somewhat unnecessary process, especially when more capable camera options are readily available.
3D cameras provide your robot with all the visual information it could possibly need, across all three axes and incorporating object rotation. This functionality comes at a price however, since 3D cameras are the most expensive cameras and also tend to be difficult to integrate and operate.
Furthermore, 3D cameras have reliability issues that make many manufacturers reluctant to embrace the technology, despite its powerhouse capabilities.
2.5D cameras occupy a sweet spot between 2D and 3D cameras, both in terms of cost and capabilities. Capable of determining the height of objects, 2.5D cameras are ideal for scenarios in which objects differ in height and when items need to be stacked. Considerably less expensive than their 3D counterparts and considerably more capable than 2D cameras, 2.5D cameras are often an ideal fit for a wide range of applications—especially applications where 3D cameras would be expensive overkill.
That said, not all 2.5D vision systems are the same.
Some 2.5D systems are easier to set up and calibrate than others, some must be attached directly to your cobot, which restricts their capabilities, and some come with software that is, at best, clunky.
Give your cobot Eyes
Meet the newly released OnRobot Eyes—a brand new 2.5D camera and vision system that can be used on all major collaborative and light industrial robot arms. Designed with ease-of-integration and -use in mind, Eyes brings all the benefits of robot vision to your operations along with some unique capabilities and features.
In particular, Eyes can be mounted externally, which brings increased versatility to your vision setup. Competing camera systems are either integrated directly into your robot arm or have to be attached to your robot's wrist to function; Eyes can be mounted anywhere within your production cell.
External mounting eliminates the issue of cables running alongside your robot. It also allows you to optimize cycle time, because Eyes can take care of image capture and processing while your robot is working on another operation.
Further, while competing camera systems often require a time-consuming calibration process, Eyes can be calibrated using just one picture, reducing the integration barrier.
OnRobot Eyes also provides seamless integration with OnRobot's existing product range, including our RG and vacuum grippers. Find out more
Contact our experts to learn more about OnRobot Eyes.

Slik gir du vekst til virksomheten med samarbeidsapplikasjoner
Takket være stadig smartere og mer fleksible verktøy kan roboter nå arbeide med høyere hastighet, styrke, sikkerhet og presisjon, og dermed håndtere en rekke oppgaver, samtidig som de maksimerer avkastningen på investeringene. Les mer om hvordan du kan øke produksjonshastigheten og senke kostnadene ved å laste ned vår eBok.
HENT DEN KOSTANDSFIRE eBOKEN
|
![]() |
