Schneider Electric Increases Safety
![]() |
Schneider Electric Increases SafetySee all Off-the-Shelf Solutions The company, committed to the pursuit of excellence and the adoption of cutting-edge technologies, decided to explore the possibilities of collaborative robotics at its Valencian plant with CFZ Cobots. After a period of testing and demonstrating the capabilities to the production department, the company decided to opt for a fully collaborative solution, combining Universal Robots' technology with OnRobot's collaborative applications.
The Challenge "We had a completely manual process, and the opportunity arose to automate it for productivity. We chose to make it collaborative for the productivity, as it is much more flexible than any other application, and, above all, for the safety and ergonomics they bring to the production line," says Daniel Ros, Industrial Manufacturing Engineer at Schneider Electric. "They also take up much less space than industrial robots, as they don't need any barriers.
The Solutions The first solution sought to bring efficiency to relay forming work. Equipped with an RG6 gripper, the robot picks up the finished relays and takes them to the tool, completing an operation that was previously done manually. "The first challenge we faced was to realise a 100% collaborative application where the robots would work and work with the person, in the same space, at the same time," says Javier Mizrahi, Process Automation & IT Engineer Industrialisation Assembly Process & Automation at Schneider Electric of Schneider Electric. "The OnRobot gripper allows us to have the flexibility to, in some positions, pick up four relays, and in other positions, pick them up one at a time, and take them to the forming station and then hand them over to the operator," says Ros. Once the first solution had been implemented, the company faced the challenge of automating the end of a new production line, which required the dual function of picking up empty buckets and filling them with finished products. To do this, two grippers were attached to the end of the arm using a Dual Quick Changer, which services a VGC10 electric vacuum gripper and an RG6 gripper. "We were faced with the possibility of using collaborative tooling again, but with the added challenge of reducing risk and improving operator ergonomics," says Mizrahi. "The dual grip was very useful for us, on the one hand, to pick up the buckets from the transport trolley and place them in the working area with the vacuum tool. On the other hand, the gripper has the flexibility to pick up one or two devices, place them in the tray and perform other manipulations, such as unloading unrecognised products on the bad belt. Incorporating a vacuum tool that does not require a compressor or air supply helped to reduce application risks. The gripper picks up and releases the pails in the same action, increasing efficiency and reducing cycle time, and is easy to move and program, achieving greater production flexibility. The transition to the new collaborative robotic applications was gradual and involved a previous phase of training about its advantages and benefits in the daily work of the operators, as it allows them to be involved in tasks of greater value and responsibility.
The Benefit With the safety of the production line assured, Schneider Electric has seen the benefits of collaborative applications in factors such as productivity and risk reduction in the manufacturing environment. "At Schneider Electric, the return on any investment we have to make must always be less than two years, but if you don't satisfy other indicators, such as safety or ergonomics in the workplace, it won't be possible to go ahead," concludes Daniel Ros.
About Schneider Schneider Electric is a world-leading industrial group in the digital transformation of energy management and automation. One of its six factories in Spain is located in Meliana, Valencia. In its 21,000 m2 of surface area, more than 11 million units of low-voltage electrical switchgear are produced every year, mainly earth leakage circuit breakers, making it the most important factory of the Schneider Electric group for this type of technology. |
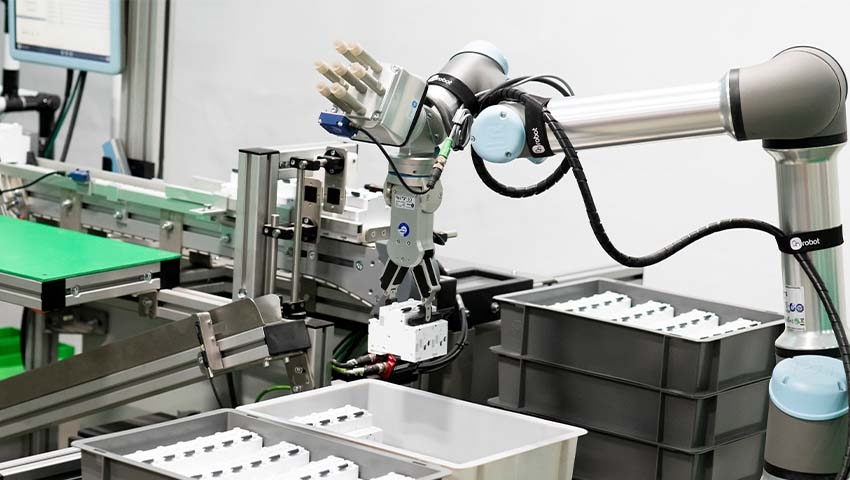
Schneider Electric Increases Safety
The company, committed to the pursuit of excellence and the adoption of cutting-edge technologies, decided to explore the possibilities of collaborative robotics at its Valencian plant with CFZ Cobots. After a period of testing and demonstrating the capabilities to the production department, the company decided to opt for a fully collaborative solution, combining Universal Robots' technology with OnRobot's collaborative applications.
The Challenge
"We had a completely manual process, and the opportunity arose to automate it for productivity. We chose to make it collaborative for the productivity, as it is much more flexible than any other application, and, above all, for the safety and ergonomics they bring to the production line," says Daniel Ros, Industrial Manufacturing Engineer at Schneider Electric. "They also take up much less space than industrial robots, as they don't need any barriers.
The Solutions
The first solution sought to bring efficiency to relay forming work. Equipped with an RG6 gripper, the robot picks up the finished relays and takes them to the tool, completing an operation that was previously done manually.
"The first challenge we faced was to realise a 100% collaborative application where the robots would work and work with the person, in the same space, at the same time," says Javier Mizrahi, Process Automation & IT Engineer Industrialisation Assembly Process & Automation at Schneider Electric of Schneider Electric. "The OnRobot gripper allows us to have the flexibility to, in some positions, pick up four relays, and in other positions, pick them up one at a time, and take them to the forming station and then hand them over to the operator," says Ros.
Once the first solution had been implemented, the company faced the challenge of automating the end of a new production line, which required the dual function of picking up empty buckets and filling them with finished products. To do this, two grippers were attached to the end of the arm using a Dual Quick Changer, which services a VGC10 electric vacuum gripper and an RG6 gripper.
"We were faced with the possibility of using collaborative tooling again, but with the added challenge of reducing risk and improving operator ergonomics," says Mizrahi. "The dual grip was very useful for us, on the one hand, to pick up the buckets from the transport trolley and place them in the working area with the vacuum tool. On the other hand, the gripper has the flexibility to pick up one or two devices, place them in the tray and perform other manipulations, such as unloading unrecognised products on the bad belt.
Incorporating a vacuum tool that does not require a compressor or air supply helped to reduce application risks. The gripper picks up and releases the pails in the same action, increasing efficiency and reducing cycle time, and is easy to move and program, achieving greater production flexibility.
The transition to the new collaborative robotic applications was gradual and involved a previous phase of training about its advantages and benefits in the daily work of the operators, as it allows them to be involved in tasks of greater value and responsibility.
The Benefit
With the safety of the production line assured, Schneider Electric has seen the benefits of collaborative applications in factors such as productivity and risk reduction in the manufacturing environment. "At Schneider Electric, the return on any investment we have to make must always be less than two years, but if you don't satisfy other indicators, such as safety or ergonomics in the workplace, it won't be possible to go ahead," concludes Daniel Ros.
About Schneider
Schneider Electric is a world-leading industrial group in the digital transformation of energy management and automation. One of its six factories in Spain is located in Meliana, Valencia. In its 21,000 m2 of surface area, more than 11 million units of low-voltage electrical switchgear are produced every year, mainly earth leakage circuit breakers, making it the most important factory of the Schneider Electric group for this type of technology.
