Welcome to the Collaborative Era


How the Biggest Trend in Collaborative Automation Simplifies Deployments & Boosts Productivity
In the B.C. era (Before Collaboration, that is), automation was the sole preserve of industrial giants with massive budgets. Automation was cumbersome, inflexible, expensive, and difficult to program. Deployment time was measured in years.
The emergence of collaborative robot systems, user-friendly tooling, and intuitive programming software over the past 10-15 years has changed all that. Deployment time is now measured in days and weeks, and the technological playing field between small and mid-sized enterprises (SMEs) and the behemoths of industry has been leveled. We are now in the Collaborative Era.
Pioneered by collaborative automation companies, but since embraced by the entire robotics industry, the current Collaborative Era is one in which automation has been democratized. The traditional barriers to automation adoption have been dismantled, providing benefits for smaller companies in particular.
What is collaborative automation?
The word ‘collaborative’ conjures images of humans and robots collaborating on tasks as equal partners. This is not the case. Collaborative automation --which consists of robot arms, end-effectors, tools, accessories, and software-- are simply easy-to-use tools designed to boost human productivity across a wide range of applications from sanding and screwdriving to pick & place.
The term ‘collaborative automation’ also refers to automation systems that enable humans, robots, and end-of-arm tools to share the same workspace safely (following a standard risk assessment), without the need for extensive safety fencing or guarding. In the Collaborative Era, the old-fashioned humans-vs-robots dynamic is completely switched around, enabling humans and automation to work together.
Today, the nature of collaborative automation itself is changing, driven by the requirements of a fast-paced manufacturing sector that is also experiencing significant change, from increasing digitalization and the move towards more customizable, high mix/low volume (HMLV) production, to an increasing need for automation due to ongoing labor shortages.
The benefits of the Collaborative Era are yours for the taking, but finding the right approach is key. By combining all the best features of cobot technologies to provide the ultimate in usability and speed of deployment, the biggest trend in collaborative automation shows the way forward.
The rise of the collaborative application
The most important trend in collaborative automation today is the rise of the collaborative application solution.
Collaborative application solutions are complete, off-the-shelf solutions, that provide all the hardware, software, tools and accessories required to take on specific applications, such as palletizing, sanding, material handling, or machine tending. SMEs are application focused. We believe automation should be application-focused too.
This application-focused trend combines all that is good about collaborative automation --usability, affordability, cost savings, and flexibility—and presents it to you in a single, off-the-shelf solution. At OnRobot, we believe that this is how industrial automation was always supposed to be –intuitive, application-focused, and accessible to companies of all sizes, even those with no prior robotics experience.
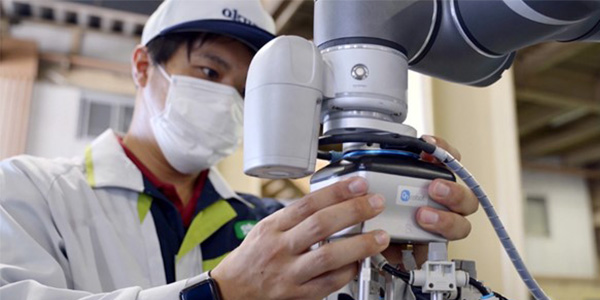
The emergence of these new application-focused solutions means that once companies have identified a task for automation, they can get everything they need in terms of tooling, accessories, and software in one package to get their collaborative cell up and running on their cobot or lightweight industrial robot arm.
Ready to use out-of-the-box, these collaborative application solutions greatly simplify the deployment process, allowing companies to deploy automation with a minimum of costly downtime and at a fraction of the cost of traditional automation deployments.
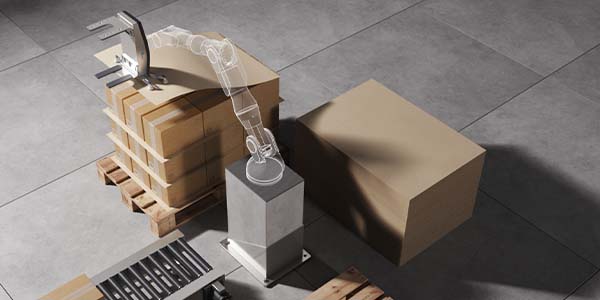
Unpacking how collaborative application solutions became the perfect fit for the changing requirements of today’s manufacturing landscape can appear challenging, especially for those new to automation.
So, let’s explore some key concepts, drivers for adoption, and the primary benefits of collaborative application solutions.
What are the key differences between collaborative and traditional industrial automation?
Unlike traditional automation, which is notoriously costly to deploy and manage, collaborative automation solutions are characterized by safety, simplicity, and both ease and speed to deployment. This makes a massive difference to your bottom line, from reduced total cost of ownership (TCO) and downtime to faster return on investment (ROI).
Traditional automation systems are best suited to low mix/high volume (LMHV) production. But the trend in manufacturing, particularly among SMEs, is towards high mix/low volume (HMLV) production, driving the need for collaborative automation. A collaborative automation system –consisting of a robot arm, end-of-arm tooling, accessories, and the software to tie it all together—can quickly and easily be adjusted to accommodate new products. And, with the appropriate tooling, the entire system can easily be switched from one application to another.
As a result, collaborative application solutions hit that sweet spot between affordability, no-fuss usability, and flexible functionality that manufacturers demand.
What does a complete collaborative application solution consist of?
Companies want automation that can be deployed quickly and that addresses specific application requirements. Call them kits, off-the-shelf packages, or ready-to-go systems: collaborative application solutions are the perfect fit for today’s fast-moving manufacturing requirements –and at a fraction of the cost of traditional automation deployments. Complete collaborative application solutions contain everything you need to perform a specific application quickly and effectively in a single package. Collaborative application solutions feature hardware, accessories and software to simplify the deployment and tie the system together. Instead of having to start your search for robots and tooling from scratch with every automation deployment, as was the case in the B.C. era, collaborative application solutions provide you with all the hardware and software you need to focus on your specific business and application requirements. OnRobot is your One-Stop-Shop for these complete, off-the-shelf solutions.
OnRobot’s Screwdriver for example, contains specially developed screwdriving hardware that’s easy to mount on any leading robot arm. Screwdriver also comes with software designed to ensure fast deployments and precise torque control (among other features).
For extra completeness, consider implementing collaborative application monitoring and analytics software. Software like WebLytics, for example, uses data gathered directly from your tooling and robot and transforms it into easy-to-understand, visualized device- and application-level intelligence, based on widely used manufacturing KPIs, such as overall equipment effectiveness (OEE).
Need to make a quick change to your collaborative automation cell, such as changing a gripper or the torque setting on a screwdriving application? Compatible with all OnRobot tools, including Screwdriver, WebLytics allows you to compare before and after performance at a glance, empowering rapid response tweaks to cell performance and ensuring that you get the most out of your collaborative automation deployment.

The final layer in a complete collaborative application solution is education and training. This speeds deployment, and feeds into the easy access and usability that is characteristic of collaborative automation in general. Learn OnRobot, for example, provides step-by-step guides to using Screwdriver, and all other OnRobot tools and components. An additional benefit of these free training resources is that you can quickly turn enthusiastic general operatives into robot operators –an upskilling that boosts worker confidence and makes the next deployment even easier than the last.
What’s driving collaborative automation adoption?
These are challenging times for the manufacturing sector. Labor shortages, global supply chain issues and economic uncertainties are stretching budgets, business continuity, and production capacity to the limit.
Collaborative automation solves critical challenges, including labor shortages. Manufacturing companies of all sizes are facing massive problems when it comes to finding and retaining labor, from unskilled and skilled operative positions all the way to production manager roles. In addition, labor is becoming increasingly expensive around the world.
A 2021 report by Deloitte and the Manufacturing Institute found that 500,000 jobs remain unfilled in US manufacturing alone. Manufacturers also reported that it is 36 percent harder to find talent today than it was in 2018, leading the report’s authors to conclude that 2.1 million manufacturing jobs could be left unfilled by 2030.
This pattern is repeated across the world from Southeast Asia to the European Union. The labor crisis in manufacturing is, at least in part, also a demographic crisis. Nearly a quarter of the US manufacturing workforce is 55 years old or older, for example. The age profile of manufacturing workers is on the rise and these workers are not being replaced fast enough.
To ease labor shortages, Dutch aluminum part manufacturer Donk Industries deployed collaborative automation on machine tending tasks, doubling CNC machine output and improving quality along the way.
Companies with adequate labor availability adopt collaborative automation for different reasons, of course, with ergonomics being a significant driver. Since collaborative automation takes care of the repetitive and potentially injurious elements of tasks, companies are deploying the technology to improve conditions for existing workers.
At the same time, manufacturers are facing rising demand driven by the explosive growth of e-commerce over recent years. More products and parts need to be manufactured than ever before to meet this demand. Unfortunately, this increasing demand is happening alongside shortages of raw materials and global supply chain pressures.
Macroeconomic uncertainties, seasonal surges in demand, tight deadlines, and the trend away from low mix/high volume (LMHV) to high mix/low volume (HMLV) production heap even more pressure on manufacturing companies.
The democratizing effect
Traditionally, robotics companies have not been good at meeting the needs of SMEs. The industrial automation systems of the B.C. era were prohibitively expensive and too complex for all but the largest companies.
Since our founding, OnRobot’s mission has been to bring the benefits of collaborative automation to SMEs by providing all the hardware and software tools required to deploy automation quickly, with a minimum of fuss, and regardless of your previous robotics experience. This means developing streamlined, easy to use products that have the same laser-like focus on the application that SMEs have.
From our end-of-arm tooling range to our specialized software for application monitoring and diagnostics to the OnRobot Learn training platform, OnRobot designs solutions with speed of deployment, ease of use, quality, and most of all with SMEs in mind.
Thanks to the rise of off-the-shelf collaborative application solutions, robotics has been simplified and democratized. Moreover, the competitive advantage conferred by automation –from increased productivity and throughput to enhanced reliability and improved quality-- is now available to companies of all sizes. This is how industrial automation in this Collaborative Era was always meant to be.
To learn more about how collaborative application solutions can benefit your company talk to one of our experts here!

Come far crescere il tuo business con applicazioni collaborative
Con il sorgere di strumenti più intelligenti e adattivi, i robot possono ora funzionare con maggiore velocità, forza, sicurezza e precisione, svolgendo un'ampia gamma di compiti, massimizzando al contempo il ROI. Per saperne di più su come è possibile ottenere una produzione più rapida a costi minori, scarica il nostro eBook gratuito.
RICEVI L'eBOOK GRATUITO
|
![]() |
